Introduction to Poultry Feed Plant
A poultry feed plant is a specialized facility dedicated to the production of high-quality feed for poultry, pivotal in the poultry farming industry. These plants play a crucial role in ensuring that the feed produced meets the nutritional requirements necessary for the healthy growth and productivity of poultry. The core functions of a poultry feed plant include sourcing raw materials, formulating balanced feed rations, and processing the feed into forms that are easy for poultry to consume and digest.
In a typical poultry feed plant, raw materials such as grains, proteins, vitamins, and minerals go through various stages of preparation and processing. Initially, these raw materials are carefully selected and tested for quality and safety. Following selection, the materials undergo grinding, mixing, pelleting, and often an additional coating step to enhance palatability and nutritional value. Each of these stages is critical for ensuring that the final product is both nutritious and safe for poultry consumption.
The significance of poultry feed plants in the industry cannot be overstated. As poultry farming continues to grow globally, the demand for consistent, high-quality feed rises correspondingly. This feed is necessary to achieve optimal growth rates, improve health, and increase the overall productivity of poultry, whether for meat or egg production. Poultry feed plants thus serve not only as production units but also as key contributors to the sustainability and efficiency of poultry farming operations.
Advancements in technology have further optimized the operation of modern poultry feed plants. Automation, precision formulation, and quality control measures have enhanced production efficiency and feed consistency. This technological progress ensures that poultry farmers receive a product that meets their specific requirements, maximizing the health benefits for their flocks and, by extension, their economic outcomes.
Advantages and Necessity of Poultry Feed Plants
The implementation of a poultry feed plant offers numerous advantages pivotal to the success of both small and large-scale poultry operations. One of the primary benefits of having a poultry feed plant is the consistent quality of feed it produces. This consistency ensures that poultry receive balanced nutrition, contributing to their overall health and productivity. High-quality feed is critical for the optimal growth of poultry, impacting factors such as weight gain, egg production, and overall vitality.
Cost efficiency stands out as another significant advantage of poultry feed plants. By producing feed in-house, poultry operators can substantially reduce the costs associated with purchasing commercially prepared feed. The initial investment in a poultry feed plant can be recouped over time through these cost savings. Furthermore, operators have the flexibility to formulate feeds according to specific nutritional requirements, thereby avoiding the extra expense of customized commercial feeds.
Moreover, improved poultry health directly linked to high-quality feed translates into lower mortality rates and reduced veterinary costs, thereby optimizing overall operational efficiency. Control over feed ingredients and production methods minimizes the risk of contamination and disease, creating a healthier flock and further fostering economic benefits.
The necessity of poultry feed plants extends beyond immediate tangible benefits to encompass long-term business sustainability and productivity. For large-scale operations, the ability to produce massive quantities of feed efficiently is indispensable. It not only ensures an uninterrupted feed supply but also facilitates consistent production processes. For small-scale operators, a poultry feed plant can be a strategic asset to encourage growth and scalability, allowing them to compete more effectively in the market.
In conclusion, adopting a poultry feed plant is a strategic decision that offers unparalleled advantages in terms of feed quality, cost efficiency, and poultry health. Its necessity is underscored by the continuous benefits it yields, supporting the sustainability and productivity of poultry operations of all sizes.
Key Processes in Poultry Feed Production Line
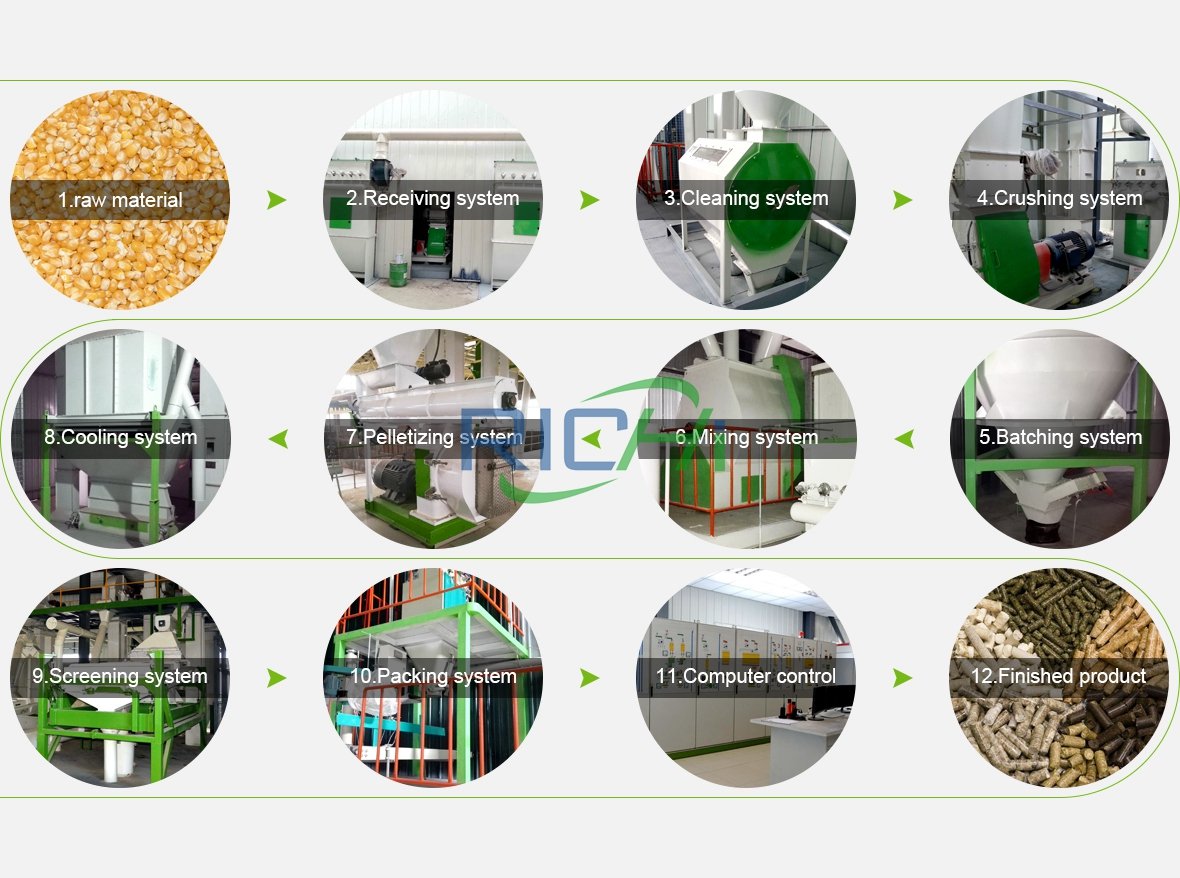
The production of high-quality poultry feed is a multifaceted process that involves several critical stages. Each of these stages contributes significantly to ensuring the nutritional integrity and overall quality of the final feed product. The initial stage in a poultry feed plant is the receiving and cleaning of raw materials. This step involves the careful examination and preparation of ingredients, removing impurities and contaminants to ensure that only the best materials proceed to the next stage.
Following this, the raw materials undergo grinding, a process essential for breaking down the feed components into smaller, uniform particles. Grinding not only enhances the digestibility of the feed but also facilitates the subsequent mixing stage. During mixing, various raw materials are blended thoroughly to achieve a homogeneous mixture. This ensures that the nutrients are evenly distributed, providing consistent nutrition in every pellet produced.
Pelletizing (main equipment: https://www.richimanufacture.com/poultry-feed-pellet-machine-price/) is the next crucial phase, during which the mixed feed is conditioned with steam and then pressed through a die to create pellets. This process binds the feed ingredients together, improving their stability and bulk. Pelletizing also assists in the elimination of pathogenic microorganisms, thereby enhancing feed safety.
Post-pelletizing, the feed pellets enter the cooling stage. Cooling is vital as it reduces the temperature and moisture content of the pellets, preventing spoilage and maintaining pellet integrity during storage. After cooling, the feed undergoes screening, a process designed to sift out and recycle fines and broken pellets, ensuring only uniform, high-quality pellets are packaged.
The final stage in the poultry feed production line is packaging. Packaging the feed accurately and efficiently is crucial to preserving its quality and facilitating ease of handling and transportation. In summary, each step in the feed production process – from raw material preparation to packaging – plays a pivotal role in maintaining the high standards expected from a modern poultry feed plant.
Identifying the Most Important Process
The functionality of a poultry feed plant is determined by several interconnected processes. Among these, the pelletizing stage stands out as a pivotal phase that directly impacts the quality, consistency, and nutritional value of the final feed product. Understanding the significance of pelletizing involves recognizing its role in converting finely ground raw materials into uniform, compact feed pellets suitable for poultry consumption.
The importance of the pelletizing process lies in its ability to enhance feed conversion efficiency. When raw ingredients are compacted into pellets, it not only facilitates ease of handling and transportation but also ensures that the feed is dense and nutrient-rich, thereby supporting optimal growth conditions for poultry. This uniformity in feed prevents selective feeding, ensuring that all components of the diet are consumed uniformly, leading to balanced nutrition.
To optimize the pelletizing process, meticulous attention should be paid to parameters such as moisture content, temperature, and the conditioning time of the feed mash before it enters the pellet mill. Correct moisture levels are crucial for achieving the right consistency and binding properties of the pellets. Equally, maintaining an appropriate temperature during conditioning helps in gelatinizing starches, which acts as a natural binder improving pellet integrity.
A common pitfall during the pelletizing stage is neglecting the maintenance and calibration of the pellet mill. Overlooking this aspect can lead to unequal pellet sizes, reduced durability, and in severe cases, mechanical breakdowns. Ensuring that the pellet mill is regularly inspected and calibrated can mitigate these risks. Additionally, maintaining a balanced formulation of the feed mix and avoiding an excess of high-fiber ingredients can prevent blockages and ensure smooth operation.
Furthermore, integrating advanced technology such as computer-aided systems in monitoring parameters during pelletizing can provide real-time adjustments, enhancing the consistency and quality of the pellets produced. This holistic attention to detail underscores why pelletizing is considered the most crucial stage in a poultry feed plant, impacting both operational efficiency and the health and growth performance of poultry.
Determining Suitable Output Capacities for Customers
When venturing into the establishment or expansion of a poultry feed plant, determining the appropriate output capacity is fundamental for aligning with business objectives. The output capacity of a poultry feed plant should correlate directly with the size of the poultry flock, production goals, and feed consumption rates. By methodically analyzing these parameters, potential customers can ensure that their investment in a feed plant is both practical and profitable.
To begin with, the flock size significantly influences the required feed production. For small-scale operations catering to backyard poultry farms or individual farmers, a feed plant with an output capacity ranging between 500 kilograms to 1 ton per hour is usually sufficient. These figures are based on typical daily feed consumption rates, with smaller flocks requiring proportionally less feed. For instance, a flock of 1,000 chickens might consume approximately 120 kilograms of feed daily, thus a smaller poultry feed plant can comfortably meet this demand while allowing for some scalability. Related machine: RICHI chicken feed pellet machine
On the other hand, medium to large-scale commercial operations, which may manage thousands of birds, necessitate a higher feed output capacity. Plants with capacities of 5 to 20 tons per hour are more suited to such extensive setups. A large-scale poultry farm housing 10,000 birds, consuming about 1,200 kilograms of feed daily, would find such capacities crucial for maintaining an uninterrupted feed supply. This ensures that production goals are met consistently, contributing to the overall health and productivity of the flock.
Moreover, production goals also play a critical role. Those aiming to expand their business or supply feed to external markets need to plan for higher output capacities. For example, if a farmer intends to not only sustain their flock of 5,000 birds but also supply feed to local farms, a plant with an output capacity of 2 to 5 tons per hour becomes much more viable. Meeting diverse production goals demands a feed plant that can adapt to varying load requirements efficiently.
In summary, understanding and calculating the required output capacity of your poultry feed plant is essential. By considering flock size, feed consumption, and production objectives, customers can select an appropriate feed plant that aligns with their operational scale, thus optimizing productivity and ensuring sustainable growth.
The Importance of Choosing the Right Manufacturer
Selecting the right manufacturer for poultry feed plant equipment is pivotal in ensuring the success and efficiency of your feed production operations. One of the foremost considerations is the quality of the equipment. High-quality machinery not only assures durability and longevity but also enhances operational efficiency by reducing the likelihood of breakdowns and repeated maintenance requirements. Investing in robust and reliable equipment can translate to significant long-term savings and consistent production outputs.
Equally important is the level of support provided by the manufacturer. Comprehensive after-sales support, including maintenance services, technical guidance, and availability of spare parts, is essential for seamless operations. A manufacturer with a strong support network enables you to address potential issues swiftly, minimizing downtime and ensuring smooth production processes. This support is invaluable for maintaining optimal feed quality and safeguarding against unexpected interruptions.
The expertise of the manufacturer in poultry feed plant design and technology also plays a critical role. Manufacturers with a proven track record and industry experience are better equipped to offer innovative solutions tailored to specific production needs. Their deep understanding of the industry’s demands and challenges positions them to provide equipment that enhances processing efficiency, reduces waste, and optimizes feed formulations.
The impact of choosing the right manufacturer extends to the overall production efficiency and feed quality. High-quality feed machinery contributes to precise mixing and grinding, consistent pellet size, and uniform distribution of nutrients in the feed. This consistency is crucial in meeting the nutritional requirements of poultry, promoting growth, enhancing health, and ultimately improving productivity.
In conclusion, selecting a reputable manufacturer for poultry feed plant equipment is a critical decision that influences the operation’s success and longevity. Prioritizing quality, support, and expertise ensures efficient feed production and upholds the high standards required for optimal poultry nutrition.
Richi Machinery stands as a preeminent figure in the poultry feed plant industry, known for its professionalism and scale of operations. As the largest pellet mill manufacturer in Henan, China, the company has carved a niche for itself through decades of commitment to quality and innovation. Founded with a vision to enhance the agricultural sector’s efficiency, Richi Machinery has evolved into a trusted name, synonymous with reliability and technological advancement.
Expertise and Experience
With years of industry experience, Richi Machinery brings unparalleled expertise to the table. The company boasts a proficient workforce that includes engineers, designers, and technical experts who collectively push the boundaries of what is achievable in poultry feed plant operations. This extensive experience ensures that Richi Machinery can cater to a diverse array of client needs, from small-scale operations to large industrial setups, with equal proficiency.
Comprehensive Product Range
Richi Machinery prides itself on an extensive product catalog that offers a wide range of machinery tailored for varied agricultural applications. At the heart of its product line are advanced pellet mills, central to the efficient functioning of any poultry feed plant. These machines are crafted with precision, ensuring optimal performance, durability, and energy efficiency. Additionally, Richi Machinery provides complementary equipment such as mixers, grinders, and conveyors, forming a comprehensive solution for poultry feed production.
Industry Reputation
The reputation of Richi Machinery within the poultry feed manufacturing sector is second to none. The company has garnered accolades for its quality products and robust after-sales support, ensuring clients receive continual assistance long after the initial purchase. By fostering long-term relationships and prioritizing client satisfaction, Richi Machinery has solidified its market position, making it a go-to choice for many in the industry.
In summation, Richi Machinery’s blend of industry expertise, extensive product range, and stellar reputation underscores its status as a leader in the poultry feed plant sector. Their contributions continue to bolster the efficiency and productivity of agricultural operations worldwide.
Conclusion
In summary, understanding poultry feed plants is crucial for anyone involved in the poultry industry. These facilities play a vital role in producing high-quality feed that meets the nutritional needs of poultry, thereby ensuring healthy and productive flocks. The comprehensive processes involved, from ingredient selection and grinding to mixing and pelletizing, are all designed to create feed that enhances the overall health and growth efficiency of poultry.
The advantages of utilizing a well-maintained poultry feed plant are manifold. They provide consistency in feed quality, which translates to better productivity and less wastage. Moreover, these plants allow for customization of feed formulas, enabling producers to cater to the specific needs of different poultry species or production stages.
Choosing a reputable manufacturer, such as Richi Machinery, is paramount in this regard. They offer not only state-of-the-art machinery but also comprehensive support and expertise, ensuring that your poultry feed plant operates at its optimal capacity. By investing in high-quality equipment, producers can guarantee consistent feed quality, operational efficiency, and long-term profitability.
Overall, the key considerations for establishing and running a poultry feed plant include understanding the essential processes, recognizing the benefits of sophisticated feed production systems, and partnering with a reliable machinery provider. By doing so, poultry producers can ensure sustainable and efficient feed production, ultimately leading to better flock health and productivity.