Investing in a pig feed mill with a capacity of 5-10 tons per hour (t/h) involves significant financial outlay for various types of equipment. While the primary objective is often to maximize production efficiency and profitability, the quality of the equipment is crucial in determining the overall quality of the feed produced. This article delves into how equipment costs in a 5-10t/h pig feed mill influence product quality and highlights the long-term advantages of investing in high-quality machinery.
Key Equipment Components and Their Costs
A 5-10t/h pig feed mill requires several essential pieces of equipment, including:
- Raw Material Handling Equipment
- Grinding Equipment
- Mixing Equipment
- Pelleting Equipment
- Cooling and Drying Equipment
- Screening and Grading Equipment
- Packaging Equipment
- Auxiliary Equipment
Cost Allocation Breakdown
Raw Material Handling Equipment
This equipment is essential for the initial stages of feed production, including receiving, cleaning, and conveying raw materials.
- Components: Silos, storage bins, pre-cleaners, bucket elevators, and conveyors.
- Cost Allocation: Generally accounts for 10-15% of the total equipment cost.
- Example Costs:
- Silos and storage bins: $50,000
- Pre-cleaners: $20,000
- Bucket elevators and conveyors: $30,000
- Total: $100,000
- Impact on Product Quality: High-quality raw material handling equipment ensures that feed ingredients are clean and free from contaminants, which is vital for maintaining the nutritional value and safety of the final product.
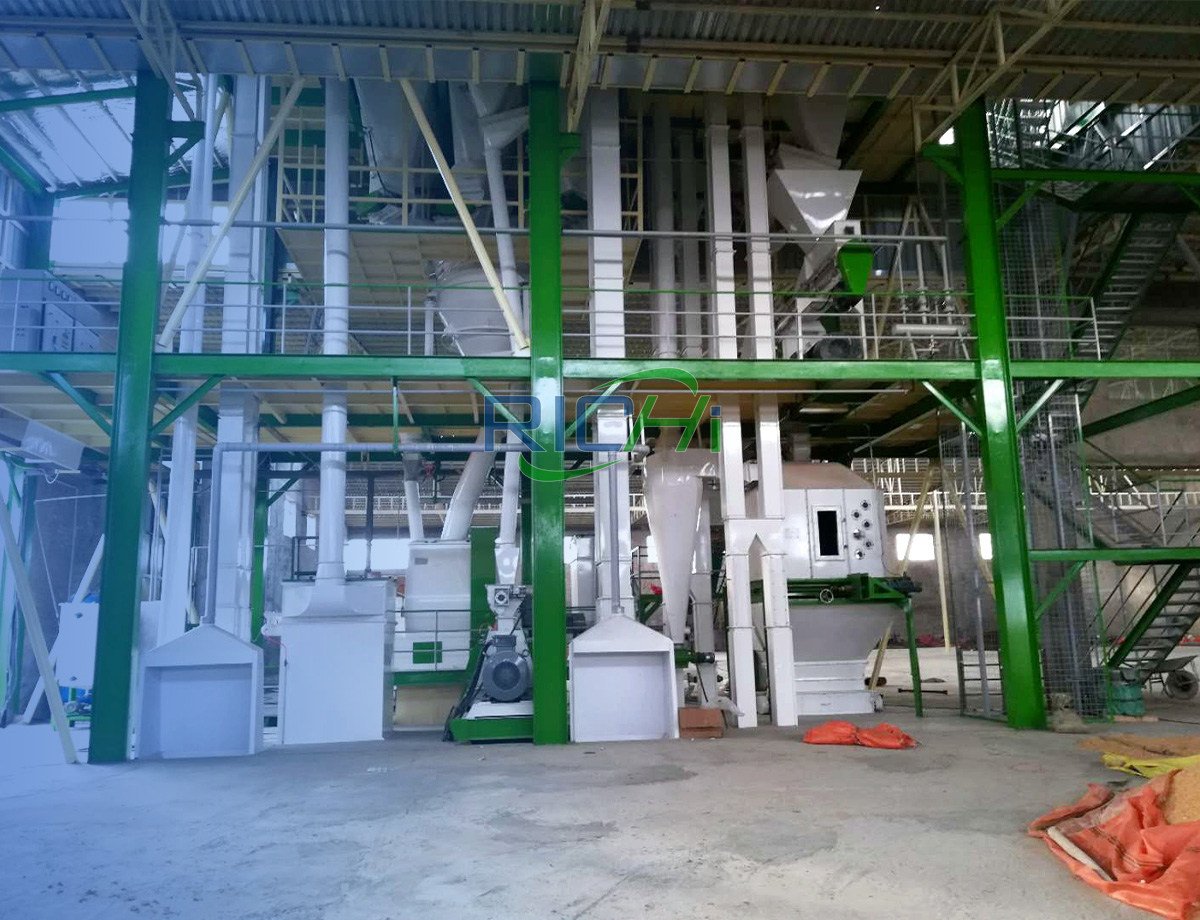
Grinding Equipment
Grinding equipment is used to reduce the size of raw materials, making them suitable for mixing and pelleting.
- Components: Hammer mills or pulverizers.
- Cost Allocation: Typically represents 10-15% of the total equipment cost.
- Example Cost:
- Hammer mills: $80,000
- Total: $80,000
- Impact on Product Quality: Efficient grinding equipment ensures that raw materials are ground to the appropriate size, which is crucial for uniform mixing and pelleting. Consistent particle size improves feed digestibility and nutrient absorption in pigs.
Mixing Equipment
Mixing equipment ensures that the ground raw materials are uniformly blended to create a consistent feed mixture.
- Components: Horizontal or vertical mixers.
- Cost Allocation: Usually accounts for 10-15% of the total equipment cost.
- Example Cost:
- Horizontal mixers: $90,000
- Total: $90,000
- Impact on Product Quality: High-quality mixers ensure that all ingredients are evenly distributed throughout the feed, preventing nutrient imbalances and ensuring that each pellet contains the correct proportions of vitamins, minerals, and other nutrients.
Pelleting Equipment
Pelleting equipment is the core of the feed production line, converting the mixed feed into pellets.
- Components: Pellet mills, conditioners, and pellet coolers.
- Cost Allocation: Generally constitutes 25-30% of the total equipment cost.
- Example Costs:
- Pellet mills: $150,000
- Conditioners: $30,000
- Pellet coolers: $50,000
- Total: $230,000
- Impact on Product Quality: Advanced pelleting equipment ensures that the feed pellets are of uniform size and density, which is important for feed intake and digestion in pigs. High-quality pellets reduce feed wastage and improve feed efficiency.
Cooling and Drying Equipment
After pelleting, the feed pellets need to be cooled and dried to ensure they are stable and ready for storage or packaging.
- Components: Counter-flow coolers, drying systems.
- Cost Allocation: Typically accounts for 10-15% of the total equipment cost.
- Example Costs:
- Counter-flow coolers: $50,000
- Drying systems: $40,000
- Total: $90,000
- Impact on Product Quality: Efficient cooling and drying systems prevent mold and bacteria growth in the feed pellets, ensuring that the feed remains safe and high quality during storage and transportation.
Screening and Grading Equipment
Screening and grading equipment is used to separate fines and ensure that the feed pellets meet the desired size specifications.
- Components: Rotary grading sieves, vibrating screens.
- Cost Allocation: Usually represents 5-10% of the total equipment cost.
- Example Costs:
- Rotary grading sieves: $30,000
- Vibrating screens: $20,000
- Total: $50,000
- Impact on Product Quality: High-quality screening and grading equipment ensures that only pellets of the correct size and quality are packaged and sold, reducing the risk of feed rejection and improving customer satisfaction.
Packaging Equipment
Packaging equipment is essential for preparing the finished feed pellets for storage, transportation, and sale.
- Components: Bagging machines, palletizers.
- Cost Allocation: Typically accounts for 5-10% of the total equipment cost.
- Example Costs:
- Bagging machines: $40,000
- Palletizers: $20,000
- Total: $60,000
- Impact on Product Quality: Efficient packaging systems protect the feed pellets from contamination and damage during storage and transportation, ensuring that the feed reaches the end user in optimal condition.
Auxiliary Equipment
Auxiliary equipment includes various supporting systems that ensure the smooth operation of the feed mill.
- Components: Dust collection systems, boilers for steam generation, electrical control systems.
- Cost Allocation: Generally constitutes 10-15% of the total equipment cost.
- Example Costs:
- Dust collection systems: $30,000
- Boilers: $50,000
- Electrical control systems: $40,000
- Total: $120,000
- Impact on Product Quality: High-quality auxiliary equipment, such as dust collection systems, improves the working environment and reduces the risk of contamination, contributing to the overall quality and safety of the feed. (Related post:animal feed plant )
Total Equipment Cost Allocation
Summarizing the cost allocation for all the equipment components yields the following:
- Raw Material Handling Equipment: $100,000
- Grinding Equipment: $80,000
- Mixing Equipment: $90,000
- Pelleting Equipment: $230,000
- Cooling and Drying Equipment: $90,000
- Screening and Grading Equipment: $50,000
- Packaging Equipment: $60,000
- Auxiliary Equipment: $120,000
Total Equipment Cost: $820,000
Long-Term Benefits of Investing in High-Quality Equipment
Consistent Product Quality
Investing in high-quality equipment ensures consistent production processes, resulting in uniform and high-quality feed pellets. This consistency is vital for maintaining the health and productivity of pigs, directly impacting the profitability of pig farming operations.
Reduced Waste and Rework
High-quality equipment minimizes the risk of production errors and reduces waste and rework requirements. This improvement enhances production efficiency and lowers overall production costs.
Enhanced Nutritional Value
Advanced grinding, mixing, and pelleting equipment ensures that the feed retains its nutritional value throughout the production process. This is crucial for meeting the dietary needs of pigs and promoting optimal growth and health.
Improved Feed Safety
Investing in equipment with advanced dust collection and emission control systems reduces contamination risks, improving feed safety. This compliance with regulatory standards is essential for animal health.
Customer Satisfaction and Brand Reputation
Consistently producing high-quality feed pellets enhances customer satisfaction and builds a strong brand reputation. Satisfied customers are more likely to become repeat buyers and recommend the feed to others, driving sales and profitability.
Conclusion
The equipment costs associated with a 5-10t/h pig feed mill significantly impact the overall product quality. By investing in high-quality, efficient equipment, feed mill operators can ensure consistent production processes, reduce waste, enhance the nutritional value of the feed, and improve feed safety. While the initial investment may be higher, the long-term benefits regarding product quality, customer satisfaction, and profitability make it a worthwhile investment. As the demand for high-quality pig feed continues to grow, investing in top-tier equipment will position feed mills for success in a competitive market.