In the competitive landscape of animal feed manufacturing, optimizing production efficiency is vital for maintaining profitability and meeting the increasing demand for high-quality feed. A 10 t/h animal feed manufacturing machine represents a significant investment for many producers, making it crucial to enhance its performance for the best return on investment. This article outlines various strategies to improve the production efficiency of a 10 t/h animal feed manufacturing machine.
1. Raw Material Quality Management
The quality of the raw materials used in feed production significantly influences the efficiency of the manufacturing process. Implementing rigorous quality management measures for incoming raw materials is essential for optimizing production efficiency.
- Ensure Proper Moisture Levels: Maintaining ideal moisture content (typically between 12-16%) in raw materials promotes better conditioning and pelleting, resulting in increased production rates and decreased wear on machine components.
- Maintain Optimal Particle Size: Crushing raw materials to an appropriate particle size (generally 2-4 mm for poultry feed) enhances the efficiency of conditioning and pelleting processes. Excessively fine particles can increase friction and energy consumption, while coarser particles may lead to poor pellet quality.
- Implement Cleaning Protocols: Effective cleaning processes to remove foreign materials and contaminants from raw ingredients protect the machine from damage and ensure consistent feed quality.
2. Preventive Maintenance
Regular preventive maintenance is crucial for maximizing the uptime and efficiency of a 10 t/h animal feed manufacturing machine. Establishing and following a comprehensive maintenance schedule helps prevent unexpected breakdowns and ensures optimal performance.
- Lubricate Critical Components: Proper lubrication of moving parts, such as bearings and gearboxes, reduces friction and wear, thereby extending the machine’s lifespan.
- Proactive Replacement of Wear Parts: Conduct regular inspections and replace wear parts like die rings and rollers to maintain consistent pellet quality and production rates.
- Thorough Cleaning: Regularly remove accumulated dust, debris, and feed residues to maintain optimal airflow and prevent blockages that can reduce efficiency.
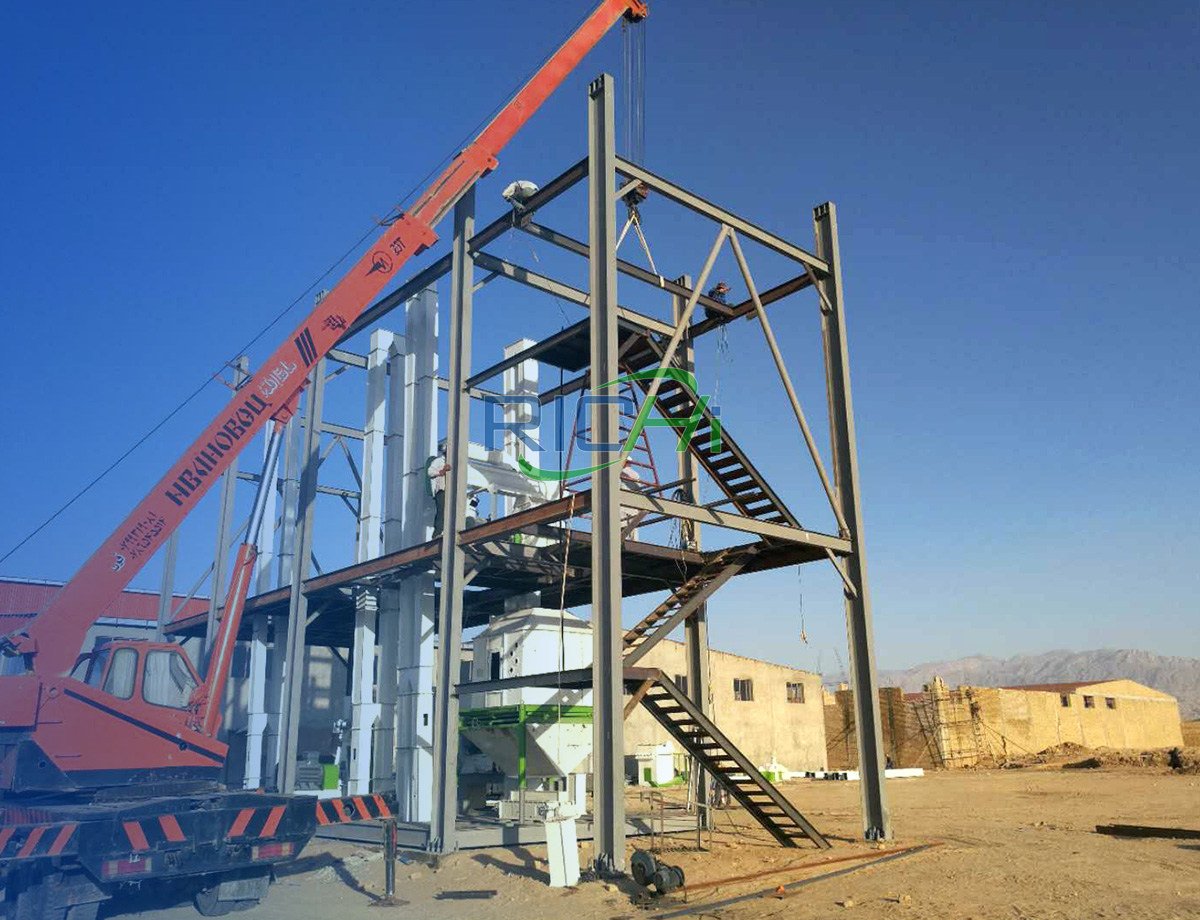
3. Process Optimization
Enhancing the feed manufacturing process can lead to significant improvements in production efficiency. By identifying and addressing bottlenecks, streamlining material handling, and implementing lean manufacturing principles, producers can elevate the overall performance of their 10 t/h animal feed making machine.
- Identify and Eliminate Bottlenecks: Address any production bottlenecks, such as slow material handling or inefficient pelleting, to ensure a smooth, continuous production flow.
- Optimize Material Handling: Reduce the number of material handling equipment and optimize the flow of materials throughout the plant to decrease energy consumption and boost efficiency.
- Adopt Lean Manufacturing Principles: Implement principles of lean manufacturing, such as continuous improvement and waste reduction, to identify and eliminate inefficiencies in the production process.
4. Automation and Control Systems
Investing in advanced automation and control systems can significantly enhance the production efficiency of a 10 t/h animal feed manufacturing machine. These systems facilitate process parameter optimization, reduce manual intervention, and ensure consistent product quality.
- Utilize Programmable Logic Controllers (PLCs): PLCs enable precise control and monitoring of critical process parameters such as temperature, moisture, and feed rate, ensuring optimal performance and product quality.
- Implement Real-Time Monitoring: Real-time monitoring systems provide valuable insights into machine performance, allowing operators to quickly identify and address issues, thereby minimizing downtime and improving efficiency.
- Automate Material Handling: Employ automated material handling systems, such as conveyors and bucket elevators, to efficiently move raw materials and finished products, reducing manual labor and minimizing error risks.
5. Employee Training and Engagement
The expertise and knowledge of machine operators and maintenance personnel are vital for optimizing the production efficiency of a 10 t/h animal feed manufacturing machine. Providing comprehensive training and fostering a culture of continuous improvement can help maximize the machine’s potential.
- Train Operators on Machine Use: Ensure operators are well-trained in the proper operation of the machine, including startup and shutdown procedures, adjusting settings, and troubleshooting common issues.
- Educate Maintenance Personnel: Offer training to maintenance staff on preventive maintenance tasks such as lubrication, cleaning, and part replacement to ensure the machine is adequately maintained.
- Encourage Employee Engagement: Promote a culture of continuous improvement by encouraging employees to share feedback and ideas for optimizing the production process. This can lead to valuable insights and innovations that enhance efficiency.
Conclusion
Enhancing the production efficiency of a 10 t/h animal feed manufacturing machine requires a multifaceted approach that addresses raw material quality, preventive maintenance, process optimization, automation, and employee engagement. By implementing these strategies, feed producers can maximize output and performance, reduce operating costs, and remain competitive in the rapidly evolving animal feed market.
Investing in the right equipment, maintenance practices, and employee training is essential for achieving optimal production efficiency. By prioritizing these factors, feed producers can ensure their 10 t/h animal feed manufacturing machine operates at peak performance, consistently delivering high-quality feed efficiently.
For details please contact: pelletizer
WhatsApp:86 138 3838 9622
Email:enquiry@richipelletmachine.com